What Are Aggregate Screens? And How Can They Help Your Mining Project?
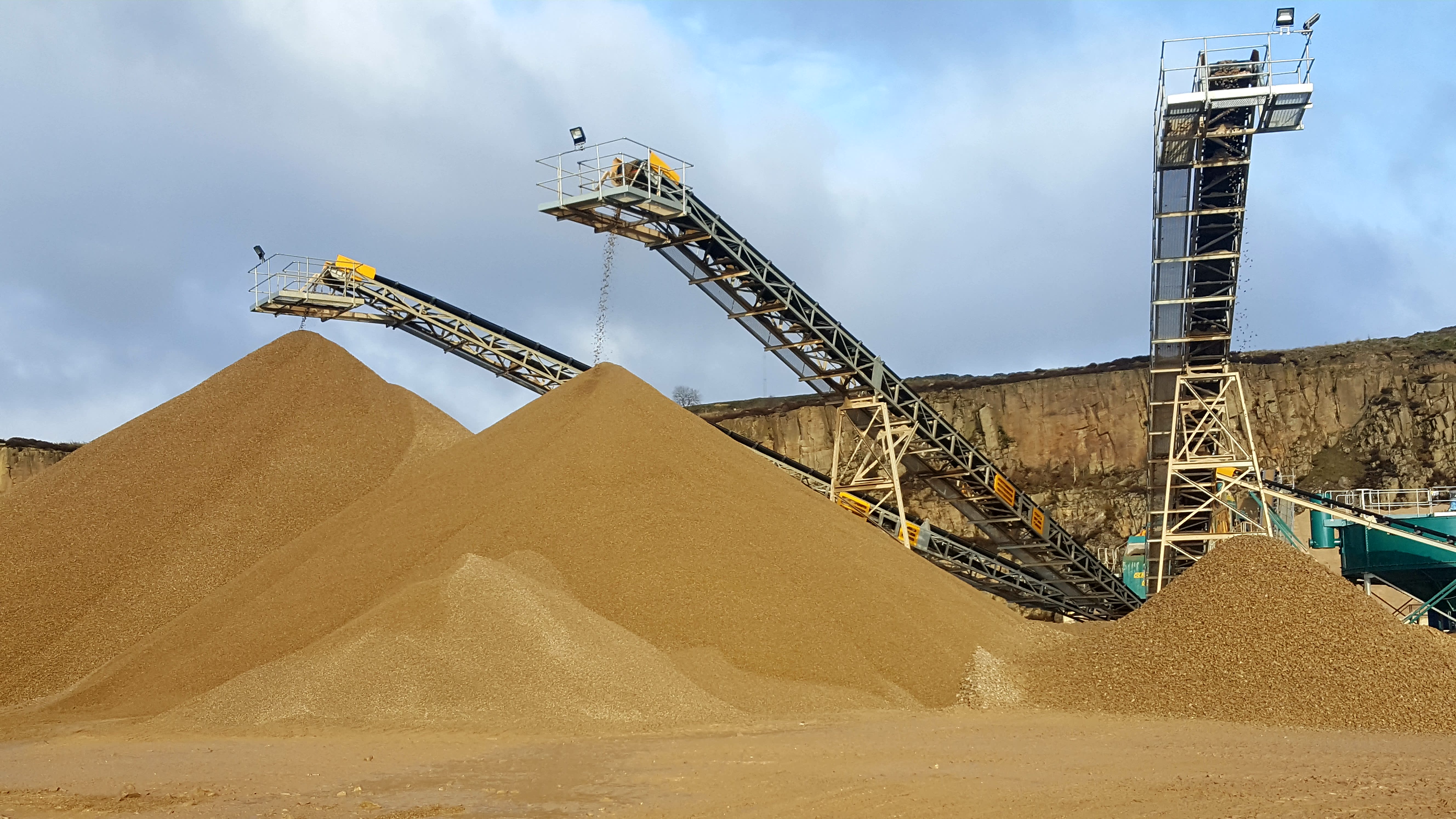
With years of experience in quarrying and aggregate supply, at Armstrongs, we understand that effective screening is crucial to delivering reliable, top-tier products.
Aggregate screening is an essential step in quarrying and construction, ensuring that only the right sizes of materials are delivered to each project, from foundation work to drainage and concrete production.
In this blog, we’ll explore the ins and outs of aggregate screening, covering its role, processes, and equipment types.
What is Aggregate Screening?
Aggregate screening is the process of sorting and separating aggregates—materials like sand, gravel, and crushed stone—into various sizes for specific applications.
It’s a fundamental process in both quarrying and construction industries, where materials must meet precise size specifications for use in everything from concrete and asphalt production to drainage systems and base layers for roads.
By using aggregate screening, we can ensure that our products meet stringent quality standards and perform optimally across a range of applications.
The primary purpose of aggregate screening is to divide raw materials into specific sizes, filtering out both fine and coarse particles as needed. This makes it possible to customise aggregate products to meet the specific demands of a project, whether that’s a 10mm gravel for pathways, a 20mm stone for concrete mixes, or much larger rock for coastal defence schemes.
How Aggregate Screening Works
In the screening process, aggregate materials are passed over vibrating or static screens, which filter and separate particles based on their size.
Different types of screens are designed to handle materials with specific properties and separate finer materials from coarser ones. This separation ensures that each batch of aggregate has uniform sizing and quality, making it ideal for its intended use.
Typically, aggregate screening starts after the materials have been extracted and crushed to a manageable size. The aggregates are then fed onto the screen surface, which may vibrate to help particles pass through openings.
Finer materials like sand fall through the smaller apertures, while larger particles are retained until they reach screens with wider openings, suited for their size. This graded process helps us at Armstrongs supply aggregates in precise sizes, tailored to meet the requirements of each unique project.
Types of Aggregate Screens
Vibrating Screens
Vibrating screens are highly efficient for separating different aggregate sizes and are widely used in high-capacity mining projects. These screens use rapid vibrations to sort and sift materials, helping to achieve precise gradation.
By constantly agitating the material, vibrating screens prevent clogging, allowing finer particles to fall through to the lower levels while larger particles are retained on the screen. This efficiency in handling large volumes makes them ideal for high-demand applications.
Static Screens
Static screens are a simple yet effective solution for smaller-scale projects or where high volumes aren’t required. Unlike vibrating screens, static screens don’t use vibrations to separate aggregates; instead, they rely on gravity to filter out the appropriate sizes.
While they’re less efficient than vibrating screens, static screens offer a cost-effective and low-maintenance alternative for aggregate screening, making them a preferred choice for more budget-conscious projects or low-maintenance operations.
Rotary Screens and Trommels
Rotary screens, often referred to as trommels, use rotating cylinders to separate aggregates. As the cylinder rotates, materials tumble within, causing smaller particles to fall through the openings, while larger pieces continue to travel along the drum.
Trommels are particularly effective in screening wet or sticky materials that might otherwise clog in vibrating screens. This setup allows them to handle a diverse range of materials, including those used in recycling and construction applications.
Types of Aggregate Screening Equipment
Aggregate Screens and Crushers
Aggregate screens work closely with crushers to produce well-graded materials that meet specific size requirements. After initial crushing, aggregates are screened to ensure uniformity and meet precise project needs.
Crushers reduce large rocks into smaller sizes, while screens refine those sizes further, removing any oversized or unwanted particles. Together, they form an essential partnership in the production of high-quality aggregates.
Grizzly Screens
Grizzly screens are unique in that they act as a preliminary filtering device before aggregates reach the crushers. They use a series of heavy-duty bars with spacing designed to allow only smaller particles through, filtering out larger materials that may not need crushing.
This setup reduces the load on crushers and prevents oversized rocks from damaging equipment, making grizzly screens invaluable in mining applications where initial sizing is necessary.
Decks and Sizing in Screening Equipment
Multi-deck screens are equipped with multiple layers, or decks, to separate aggregates into different size categories. Each deck has openings sized specifically to allow only aggregates of a certain size to pass through.
This setup makes multi-deck screens highly versatile, enabling precise sizing for various applications and ensuring consistency across different aggregate products. Multi-deck screens are essential for producing uniform materials like sand, gravel, and crushed stone, tailored to fit exact specifications for projects.
Aggregate Screen Sizes and Their Uses
Common Aggregate Screen Sizes
In the aggregate industry, materials are classified by size to meet specific construction needs. Common aggregate screen sizes range from fine sands of less than 2mm to large stones exceeding 100mm.
Fine aggregates, such as sand, are essential for creating mortar and concrete mixtures, providing the necessary fill and stability. Medium-sized aggregates, like our 10mm and 20mm options, are ideal for pathways, driveways, and concrete production.
Larger aggregates, such as 40mm and 75mm stones, are used for drainage applications, sub-base layers, and structural fills. By utilising precise screening of aggregates, we ensure each size category meets industry standards and project specifications.
Selecting the Right Screen Size for Your Project
Choosing the appropriate aggregate screen size is crucial for the success of your project. The size of the aggregate impacts the strength, durability, and appearance of the finished construction.
For instance, fine sands (0-2mm) are perfect for mortar and render, providing a smooth finish. Medium aggregates (10mm to 20mm) are commonly used in concrete mixes and as pipe bedding, offering a balance between strength and workability.
Larger aggregates (40mm to 150mm) are suitable for sub-base materials, drainage solutions, and erosion control structures like riprap and gabions.
At Armstrongs, we utilise advanced aggregate screens to sort materials accurately, ensuring you receive the ideal aggregate size for your specific needs.
Applications by Screen Size
Our range of aggregates at Armstrongs is meticulously screened to cater to various applications:
- 0-2mm Sand: Ideal for mortar and render, providing a fine texture for smooth finishes.
- 0-4mm Sand: Used in concrete production and for block paving, offering a slightly coarser texture.
- 10mm Aggregate: Suitable for pathways, driveways, and concrete production, providing stability and a uniform appearance.
- 20mm Aggregate: Commonly used in concrete mixes and as pipe bedding, offering increased strength.
- 40mm Aggregate: Used for sub-base layers and Type B drainage material, providing structural support.
- 75mm Aggregate: Ideal for sub-base and drainage applications, offering excellent load-bearing properties.
By employing precise aggregate screening, we ensure that each product meets the necessary specifications for its intended use, enhancing the quality and longevity of your construction projects.
Benefits of Aggregate Screening in Quarrying
Enhanced Efficiency
Effective aggregate screening significantly boosts efficiency in quarrying operations. By quickly sorting materials into designated sizes, we reduce processing time and improve productivity.
This streamlined approach allows us to meet high-demand schedules and provide our clients with timely deliveries. Efficient screening in quarrying ensures that resources are utilised optimally, minimising waste and maximising output.
Consistent Product Quality
Maintaining consistent quality in our aggregates is paramount. Through precise aggregate screening, we ensure that each batch meets strict size and quality standards.
Consistent aggregate screen sizes are essential for the performance of construction materials like concrete and asphalt.
Uniform aggregates contribute to the structural integrity of projects, reducing the risk of material failure and ensuring long-term durability.
Cost and Time Savings
Using the right aggregate screening equipment leads to significant cost and time savings. By accurately separating materials, we reduce the need for reprocessing and minimise material wastage.
Efficient quarrying screening equipment allows us to handle large volumes effectively, lowering operational costs. These savings are passed on to our clients, providing high-quality aggregates at competitive prices and ensuring projects stay within budget and on schedule.
At Armstrongs, we’re dedicated to providing top-quality aggregates tailored to your project’s specific needs. Our expertise in aggregate screening enables us to deliver products that meet the highest industry standards, ensuring the success and longevity of your construction endeavours.
Armstrongs’ Aggregate Screening Capabilities
Our Aggregates and Aggregate Screen Sizes
At Armstrongs, we offer a comprehensive range of quarry aggregates carefully screened to meet the diverse needs of our clients. Our product range includes fine sands, like 0-2mm sand for mortar and render, versatile 10mm aggregates for pathways and driveways, and large 150mm gabion material used in civil engineering projects.
By providing multiple aggregate screen sizes, we ensure that each product meets the highest quality standards for specific applications, from foundational layers to decorative pathways.
Our aggregate screening methods enable us to deliver precisely sized materials for construction, landscaping, and infrastructure projects.
Quality Assurance and Custom Sizing
Quality is at the heart of everything we do at Armstrongs. Our team uses a rigorous quality control process throughout each stage of production, ensuring consistency and reliability across our aggregate screens.
We’re equipped to provide custom sizing, allowing us to meet unique project specifications and deliver materials that align with your construction needs. Our aggregate screening technology enables us to fine-tune products to exact client requirements, from exact screen sizes to tailored material blends.
This commitment to quality ensures that we meet or exceed industry standards, providing clients with dependable, durable aggregates.
Aggregate Screens and Environmental Considerations
Reducing Waste with Effective Screening
At Armstrongs, we recognize the environmental impact of quarrying and take steps to reduce waste through efficient aggregate screening processes. By using advanced screening of aggregates technology, we sort materials accurately, maximising resource use and minimising surplus.
This efficiency not only improves sustainability but also ensures that our quarrying processes are as environmentally responsible as possible. Reducing waste through effective screening is part of our commitment to responsible resource management and eco-conscious operations.
Sustainable Mining Practices
Sustainability is central to Armstrongs’ quarrying philosophy. Our commitment to eco-friendly practices extends to the use of mining screening equipment that minimises environmental impact.
By using advanced aggregate screening machinery, we optimise energy use and maintain strict controls on our production footprint. We continually seek ways to improve our processes, integrating sustainable practices that preserve natural resources, reduce emissions, and support the longevity of our quarries.
Our dedication to sustainability ensures that we provide high-quality materials while respecting the environment.
Aggregate Screens and Their Uses FAQs
What is aggregate screening?
Aggregate screening is the process of sorting and separating aggregate materials by size to ensure they meet specific requirements for construction and infrastructure projects. This process uses various screen types to filter materials and ensure a consistent, reliable product.
What types of aggregate screening equipment are available?
There are multiple types of aggregate screening equipment used in mining and quarrying, including vibrating screens for high-capacity sorting, rotary screens for efficient circular motion, and grizzly screens for pre-screening large materials. Each type is suited to different applications and material types.
How do aggregate screens work with crushers?
Aggregate screens and crushers work together to refine materials. Screens sort the materials into specific sizes, which are then processed further by crushers to achieve consistent, high-quality aggregates ready for use in construction.
What are common aggregate screen sizes?
Common aggregate screen sizes range from fine sands under 2mm for mortar mixes, up to larger sizes like 40mm and 75mm for drainage layers and structural fills.
Each size has distinct applications suited to the needs of various construction projects.
How can I choose the right screen for my mining project?
Selecting the right screen size and equipment type depends on the specifics of your project, including material type, intended application, and production volume.
Consulting with aggregate experts, like Armstrongs, helps ensure that your screening setup matches your project requirements.